Hybrid (In Person at the Boston Park Plaza OR Virtual)
14 A and B – Flexure Mechanism Design and Evaluation of Motion Constraints – Parts 1 and 2
Dr. Stuart T. Smith (University of North Carolina – Charlotte)
Dr. Marijn Nijenhuis (University of Twente)
Tuesday, November 14, 2023
8:30 AM – 12:30 PM (EST USA) – Part 1
Tuesday, November 14, 2023
2:00 PM – 6:00 PM (EST USA) – Part 2
Flexure-based stages and mechanisms are used in precision motion control and alignment applications including lithography, metrology instruments, mass balances, telescope mirror positioning, and medical devices. Flexure mechanisms offer frictionless, zero play, limited or zero hysteresis, and contaminant free motion in ranges of nanometers to millimeters and potentially 180° rotations. Their design needs consideration of numerous parameters such as volume, dynamics, lifetime, stresses in the flexural elements, range of travel, parasitic motion, rotation center shift, and load bearing capability. Therefore, the design process requires a vast range of design and analysis approaches to ensure its functionality.
Part I: Basics of Flexure Mechanism Design, Implementation, and Mobility Assessment
Flexure joint and mechanism examples classified by their degrees of freedom
Manufacturing processes and assembly techniques
Parasitic errors in motion such as arcuate motion (foreshortening) and center shift
Types of actuators and their coupling to the mechanism, levers, lost motion, sensors, and damping techniques
Lagrangian – energy dynamics modeling
Damage assessment (number of cycles to failure)
Part II: Interactive Web Application for Mobility Visualization Using Flexible Multibody Analysis
Mobility analysis using the equation alone does not provide quantitative information about the consequences of the over and under constraints due to their directional dependence and complex geometries. To address the need to quantify these consequences, a multibody kinematic approach is used to visualize the free motions and constraining forces and moments in a given design, and this is discussed in Part II of the tutorial.
Part II initially focuses on a multibody formulation which uses kinematic equations for deriving a Jacobian matrix that relates coordinates and deformations. This helps to capture orientation dependent behavior of constraints in a mechanism. Later, the audience will be provided with an interactive web application for modeling and visualizing the mobility of flexure mechanisms. A brief introduction to a full multibody software which provides quantitative numbers indicating the effect of overconstraints on stresses and frequency modes will also be given. This can be helpful when considering design trade-offs between requirements such as stress of over-constraint competing against the stress of an off-axis load.
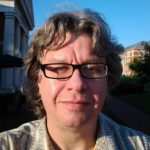
Dr. Stuart Smith has been working in engineering since 1977 as a factory maintenance apprentice with Miles Redfern Ltd (UK). He is now a Professor of Mechanical Engineering in the Center for Precision Metrology at UNC Charlotte. Throughout the years his major focus has been the development of machines, instrumentation and sensor technologies primarily aimed towards the challenges of atomic scale discrimination and modifications. This work has resulted in the formation of four manufacturing companies, twenty patents, over a hundred journal publications, and the (co)authorship of five books.
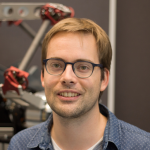
Dr. Marijn Nijenhuis is an Assistant Professor and the Chair of Precision Engineering at the University of Twente in the Netherlands. He holds a doctorate degree from the same university on the topic of the nonlinear analysis of flexure mechanisms. His research focuses on the analytical and numerical modeling of mechanical systems for the purpose of design and control. Research interests include flexible multibody dynamics and (electro)mechanical metamaterials.