In Person ONLY at the Boston Park Plaza
12 A and B – -Precision Mechatronics Case Studies – Parts 1 and 2
Dr. Johannes P. Vermeulen (ASML/TU Eindhoven)
Dr. Dannis M. Brouwer (University of Twente)
Monday, November 13, 2023
2:00 PM – 6:00 PM (EST USA) – Part 1
Tuesday, November 14, 2023
2:00 PM – 6:00 PM (EST USA) – Part 2
DESIGN PRINCIPLES FOR PRECISION MECHATRONICS
Despite the revolutionary advances in Precision Engineering and Mechatronics in the last few decades, the importance of design for repeatability, has remained equally important as stressed earlier by Clayton Teague, Chris Evans, Pat McKeown, and Wim van der Hoek, for example, through kinematic design to guarantee the integrity of high accuracy parts, such as wafer chucks, metrology frames, sensors and projection optics. To further increase control bandwidth, it became beneficial in the 2010 timeframe to introduce the concept of over-actuation to avoid excitation of internal mode shapes at high-acceleration setpoint. Although seemingly contradictory to kinematic design, over-actuation does not necessarily affect repeatability, provided that ‘force’ actuators are used with very limited residual non-linearities in position and current. Also, the importance of thorough understanding of the relevant dynamics in the design has not changed since the analyses of cam shaft mechanisms in the 1950s, but focus has shifted from creating favorable time responses to shaping of frequency response functions (FRFs). Driven by developments in optical storage, such as CD and DVD players, and later on semiconductor equipment in the 1990s, the understanding of superposition of mode shapes and optimal actuator and sensor placement to ‘shape’ the dynamic FRFs was key to robust controller design in combination with good performance. Recently, the implementation of passive damping was added to realize suppression of amplifications at resonances and thereby, sufficient exponential decay of undesired vibrations in uncontrolled DoFs. Damping, which was abandoned for a long time in view of the risk of position uncertainty by hysteresis, became a new design paradigm.
As a result of increasing complexity at the component level, driven, among others, by Moore’s Law, more ‘global’ mechatronic solutions are required these days to enable better performance at reduced cost. Precision Mechatronics design these days implies ‘the balancing of complexity at the component level to control motion down to the atomic level’.
This Tutorial on Precision Engineering Case Studies will focus on ‘how to design hardware as part of a modern, precision mechatronic system’. Via numerous examples and case studies, along with the underlying physics, Precision Engineering design principles for deterministic machine behavior will be explained in many detail (see below and https://www.dspe.nl/knowledge/dppm-cases/). Part 1 covers the principles: 1) Kinematic design, 2) Design for stiffness, 3) Lightweight design, 4) Design for damping, and 5) Design for symmetry; Part 2 touches upon the principles: 6) Design for low friction and hysteresis, 7) Design for low sensitivity (short timescale), 8) Design for stability (long timescale), 9) Design for load compensation, and 10) Design for minimal cost and complexity.
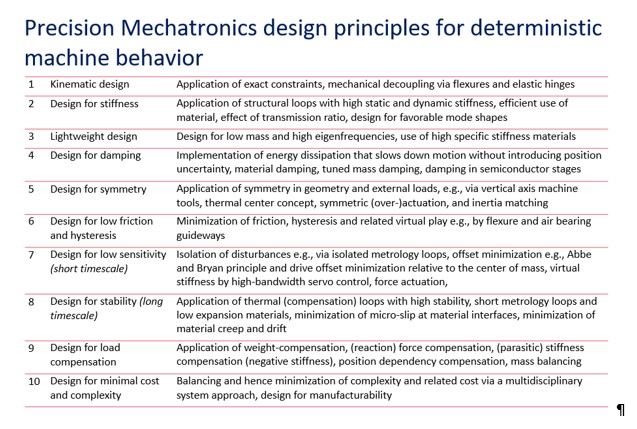
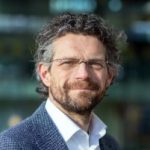
Dr. Hans Vermeulen received his M.Sc. degree, MTD Post-Master’s degree and Ph.D. degree at the Eindhoven University of Technology in the Netherlands. From 1999-2007 he was working with Philips Electronics, of which two years in Pittsburgh, PA, where he worked on EUV and Nano-Imprint lithography systems. In 2007, he joined ASML, where he was senior research manager from 2012-2017, and senior principal architect for the EUV high-NA optics system, closely collaborating with Carl Zeiss-SMT from 2017-2023. Recently, he became strategic sourcing manager, responsible for the industrial strategy development for mechatronic modules within ASML. In 2010, he received the ASML Patent Award 2010 for most invention disclosures and patent applications company wide. He is (co)author of over 70 patent applications. He was chairman of the national R&D Work Group Mechatronics at the High Tech Systems Center at TU/e from 2011-2017. From 2015 on, he is part-time full professor at the Eindhoven University of Technology in the Control Systems Technology group – Design for Precision Engineering, with a chair in Mechatronic Systems Design. He is member of DSPE, euspen, ASPE and CIRP, and technical trainer at the High Tech Institute – Mechatronics Academy in Design Principles for Precision Engineering, Mechatronics, Dynamics and Modelling, and Passive Damping for High-Tech Systems. In 2022, he received the Prof. M.P. Koster Award for his significant contributions to the field of Mechatronics and Precision Engineering, based on oeuvre, creativity, relevance (social and commercial) and professional appearance. His research interests are in the field of extremely accurate and fast electromagnetic and piezoelectric (EUV) motion systems, superconducting linear and planar motors, distance measuring interferometry, adaptive optics, medical robotics for vascular and interventional X-ray imaging, and mechatronic equipment for X-ray beamlines.
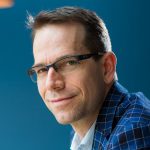
Dr. Dannis M. Brouwer received his MSc. degree in mechanical engineering in 1998, and a postmaster (PDEng) degree in mechatronic design in 2001 from Eindhoven University of Technology in the Netherlands. In 2007, he received the doctoral degree in mechanics from the University of Twente. He was appointed full Professor at the University of Twente in 2020 and is now chairing the Precision Engineering Lab. He has (co)authored over 50 refereed journal articles, 90 conference contributions and 8 patents on a variety of subjects including flexure mechanisms, kinematics, macro and micromanipulators, variable impedance robotics and precision engineering.