In Person Only
5-New Techniques for Performance Evaluation of High-Precision Single Axis Linear Positioning Systems within ASME B5.64
Moderator: Greg Vogl (National Institute of Standards and Technology)
Speakers ASME B5.64 Contributors: Stephen Ludwick (Aerotech, Inc.)
Axel Grabowski (Physik Instrumente)
Monday, October 10, 2022
8:00AM – 12:00N (PDT USA)
Linear positioning systems are utilized in wide-ranging manufacturing applications from machine tools to high-precision applications such as semiconductors and photovoltaics. New linear positioning systems exist with ranges of motion as long as several centimeters and positioning resolutions as low as several nanometers. The ability to meet high-precision manufacturing tolerances requires accurate knowledge of the positioning performance of these systems, yet a dedicated standard for evaluating the performance of high-precision single axis linear positioning systems does not exist. Existing standards for the performance of single axis linear positioning systems within machine tools (ASME B5.54-2005, ASME B5.57-2012, ISO 230-1:2012) can be difficult to apply for the performance of high-precision positioning systems that can approach the measurement uncertainty. A new standard with measurement methods specific to characterization of these stages is needed.
This tutorial outlines new techniques within a soon-to-be-published standard, ASME B5.64 (“Methods for the Performance Evaluation of Single Axis Linear Positioning Systems”), for performance evaluation of single axis linear positioning systems. ASME B5.64 was developed with input from industry, academia, and government in coordination with the American Society of Mechanical Engineers (ASME) and is planned to be published by the end of 2022. This tutorial will highlight the new methods in the standard for incremental step, in-position jitter, constant-velocity evaluation, dynamic performance, point repeatability, and servo characterization, among others. Characterization of the positioning-related errors and the stage error motions, both straightness and angular, will be covered. Participants will have opportunities to discuss the new methods and provide input for future versions of the standard with committee members.
8:00-8:15 | Overview and Motivation of Standard & Tutorial | Vogl |
8:15-8:25 | Coordinate Systems and Positioning Errors | Ludwick |
8:25-9:15 | In-Position Jitter, Move and Settle, & Step Tests | Ludwick |
9:15-9:30 | Point Repeatability | Vogl |
9:30-9:45 | Submission of Questions/Polls | |
9:45-10:15 | Break | |
10:15-10:45 | Static Positioning Accuracy & Repeatability | Grabowski |
10:45-11:15 | Dynamic Geometric Accuracies & Constant Velocity Tests | Grabowski |
11:15-11:30 | Submission of Questions/Polls & Break | |
11:30-11:45 | Discussion of Questions/Polls | Vogl & Team |
11:45-12:00 | Next Steps & Tutorial Survey | Vogl |
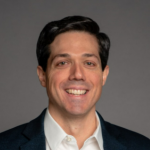
Dr. Gregory W. Vogl is a Mechanical Engineer at the National Institute of Standards and Technology (NIST) located in Gaithersburg, Maryland. He received his degrees in Engineering Mechanics from Virginia Tech, after which Greg designed, fabricated, and experimented on microelectromechanical systems as a National Research Council Postdoctoral Researcher at NIST. Greg then joined the Production Systems Group, in which he worked on standards development for machine tools and vibration metrology for accelerometers. Currently, Greg develops sensor-based solutions for real-time health assessment of components and processes within machine tools. For his contributions, Greg is the recipient of a NIST Engineering Laboratory Mentoring Award, NIST Colleagues’ Choice Award, and NIST Engineering Laboratory Outstanding Publication Award.
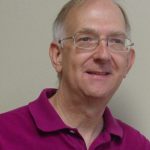
Dr. Jimmie Miller, ASPE member since 1990, is currently (25+ years) the Chief Engineer for the Center for Precision Metrology at the University of North Carolina at Charlotte. He holds an AAS degree in electronics engineering technology, a BS in both mathematics and physics and a MS (UNC Charlotte) and PhD (U Warwick) in Engineering. Interests include instrumentation, dimensional metrology, machine design and metrology, and interferometry. He was the co-recipient of the 2009 ASME Blackall Machine Tool and Gage award.
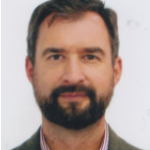
Dr. Stephen Ludwick leads the Mechatronic Research Group at Aerotech, Inc., a manufacturer of precision automation systems. He joined Aerotech in 1999 and is currently responsible for developing motion control systems and feedback control algorithms with an emphasis on the interactions between mechanical, electrical, and algorithmic components of a design. He is also an adjunct associate professor in the Department of Mechanical Engineering and Materials Science at the University of Pittsburgh, and currently serves as an Editor-in-Chief for the Precision Engineering Journal. Steve holds a B.S. degree in Mechanical Engineering & Engineering and Public Policy from Carnegie Mellon University, and S.M. and Ph.D. degrees in Mechanical Engineering from the Massachusetts Institute of Technology.
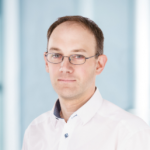
Dr. Axel Grabowski studied physics and mathematics at the University of Saarland, Germany. He received a diploma degree in physics in the field of surface science in 2000. Afterwards, his research career focused on the field of quantum optics and he continued his work at the University of Stuttgart, Germany, where he finished his Ph.D. in Physics in 2006. In the same year he joined Physik Instrumente (PI), Germany, a worldwide leading supplier of solutions in the fields of motion and positioning as a research and development engineer. These days Dr. Axel Grabowski is Head of the R&D Department Sensor Technologies at Physik Instrumente (PI). He holds several patents in the field of sensors and sensor technologies. His research and development group mainly focuses on the development of new and advanced sensor and measurement technologies ranging from single-axis to multi-axis solutions. He is an ASME member and an active member of the group working on the ASME B5.64 “Methods for the Performance Evaluation of Single Axis Linear Positioning Systems” standard.