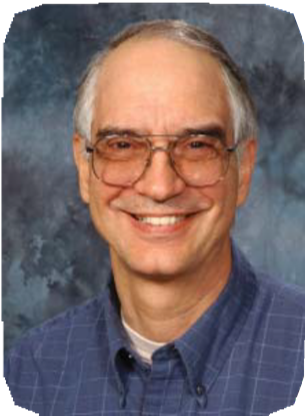
Bill Barkman began his precision manufacturing career in the early ‘70’s at the Y-12 National Security Complex. His initial work involved the development of technologies in support of Y-12’s diamond machining activities and this instilled a deterministic manufacturing mindset that has continued throughout a career that includes over 45 technical publications, 7 patents, a book titled “In-process Quality Control for Manufacturing” (Marcel Dekker, Inc., 1989), and a short course on manufacturing variability.
Bill has an extensive background in the precision manufacturing operations required for the production of nuclear weapons components and has been responsible for the development of machining and inspection systems capable of automated operations in a rigorous manufacturing environment.
Bill has also demonstrated expertise in the development and execution of collaborative partnership activities (e.g. National Nuclear Security Administration Thrust Areas for Agile Machining and Inspection, Digital Radiography, Noncontact Inspection; and the public/private Cost Effective Machining of Ceramics program). In addition, recent research projects with partners from the public, private and academic sectors have focused on cybersecurity challenges associated with the US manufacturing industrial base.
Bill would like to see the ASPE play a role in communicating the importance of establishing and maintaining information security protocols in our manufacturing community and also in encouraging a shift away from the perceived dichotomy that there is a sophisticated precision manufacturing culture with “little variation in process parameters, e.g. tool wear” and the mundane manufacturing world where “process disturbances are just a way of life and nothing can be done about it.” The first challenge can be addressed by learning to apply a “classified mindset in an unclassified environment,” while the second challenge can benefit from applying deterministic manufacturing principles to whatever extent is practical and also designing systems that are less sensitive to process disturbances, e.g. in-process tool compensation.