2022 Summer Topical Meeting
Advancing Precision in Additive Manufacturing
July 11-14, 2022
University of Tennessee, Knoxville
UTK Conference Center
Tennessee, USA
Co-chairs
John S. Taylor, University of North Carolina at Charlotte
Richard K. Leach, University of Nottingham, UK
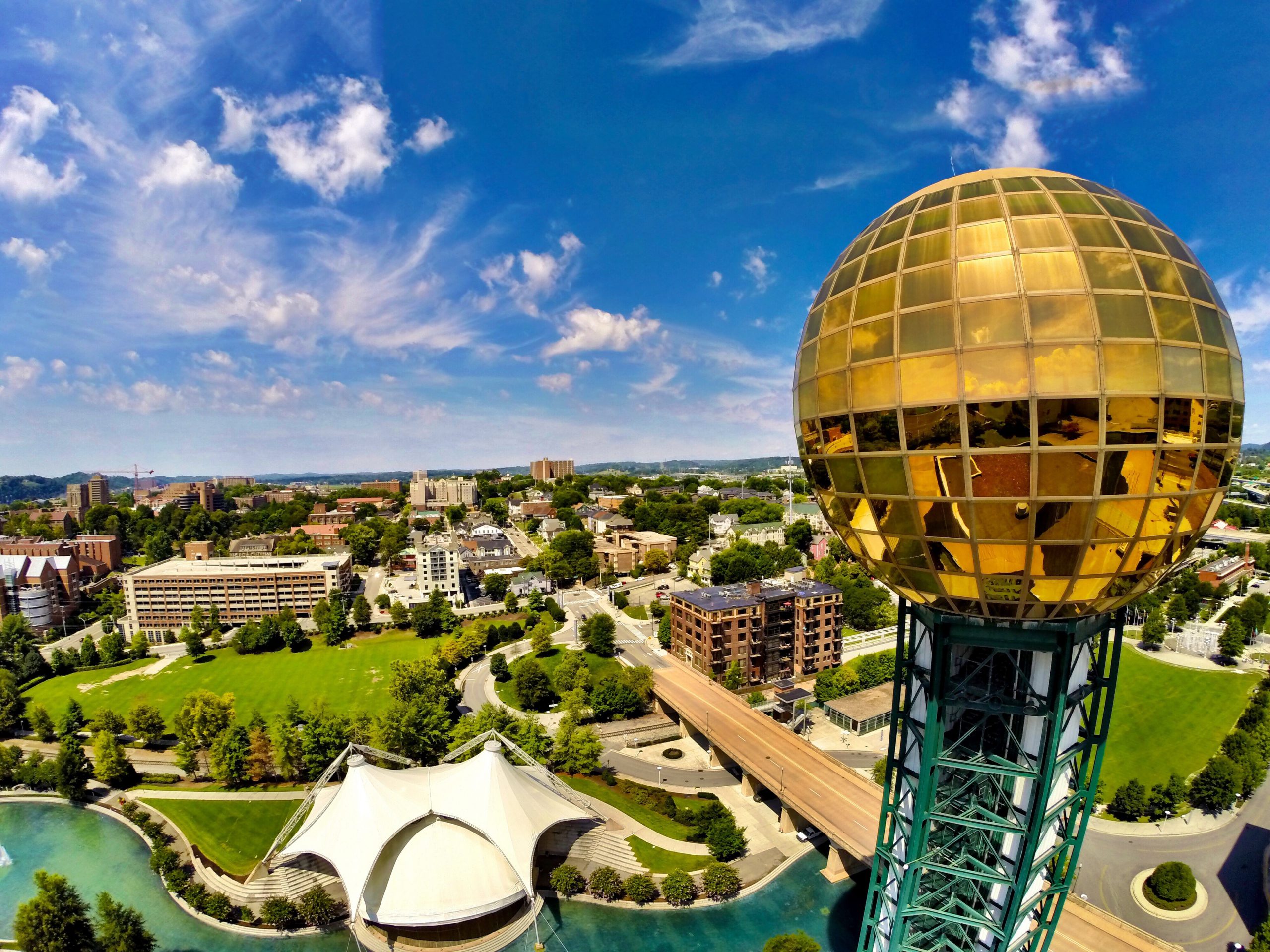
The ASPE-euspen Summer Topical Meeting: Advancing Precision in Additive Manufacturing took place in Knoxville, TN from July 11-14, 2022. The 9th installment in this annual series of topical meetings saw the intersection of additive manufacturing (AM), precision engineering, and metrology. The live on-site meeting was chaired by John S. Taylor (University of North Carolina at Charlotte), with assistance from local host Bradley Jared of the University of Tennessee, Knoxville (UT). Co-chair Richard Leach (University of Nottingham) contributed to the planning of the meeting. Broad topical coverage was enabled by a thirty-member international Organizing Committee. The meeting was held at the UT Conference Center in downtown Knoxville. Overall conference planning and management was provided by ASPE Executive Director Wendy Shearon, with logistics and audio-visual support from Attended Event Planning & Production.
The meeting received enthusiastic participation with 58 paper submissions and approximately 90 attendees, of which about half were from Europe, along with a small contingent from South Korea. While COVID introduced some challenges, disruptions were minimal and the meeting was largely uninterrupted for the majority of attendees.
Networking opportunities were provided at an Opening Reception, Conference Dinner, and Closing Reception. The conference planners gratefully acknowledge generous sponsorship from ASML and Carl Zeiss. Representatives from each sponsor gave short introductions to their companies in the opening oral session and offered to speak to any attendees or students about employment opportunities. Banners for the sponsors were displayed throughout the meeting and at all networking events.
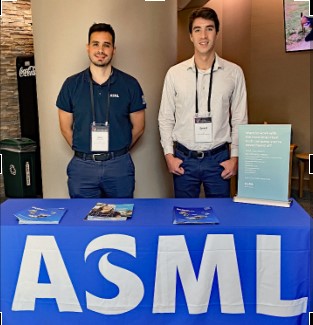
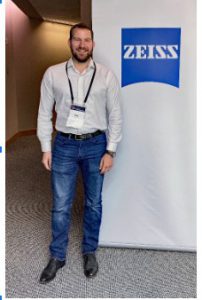
The technical interchange at the conference began with three tutorials presented on Monday. Adam Thompson (University of Nottingham) taught both “Measurement and Characterization of Metal Additive Surfaces” and “An Introduction to Measurement Uncertainty and the Guide to the Expression of Uncertainty in Measurement.” Fred van Keulen (Delft University of Technology) taught “Topology Optimization for Additive Manufacturing.” In all tutorials there was lively discussion and interchange with the attendees.
Two tours gave the attendees a view of the manufacturing expertise in the Knoxville area. The advanced manufacturing labs of Professors Bradley Jared and Tony Schmitz at UT showed how students were combining robotics, metrology and additive manufacturing, such as directed energy deposition (DED). One example featured a hybrid cell with KUKA robots, fringe-projection scanning metrology, CNC mills, and wire-arc DED AM. Another cell featured process stability studies of thick-walled DED components. Other labs included metal laser-powder bed fusion and polymer fused filament machines, with access proved to all UT students.
Later in the day, the attendees rode buses to the Manufacturing Demonstration Facility of Oak Ridge National Laboratory. This is a large, internationally-recognized facility dedicated to both additive manufacturing and advanced subtractive manufacturing. After a brief introduction by the MDF’s director, William Peter, the attendees were divided into thirteen groups to be rotated among as many tour stops. The technologies ranged from very large-scale DED to powder bed fusion where feedstock materials included superalloys, polymers, and ceramics. Workpiece sizes ranged from “breadbox” up to multiple meter-class, such as for automotive and aircraft wingtip applications. Scott Smith, Intelligent Machine Tools group leader, hosted the stop at advanced manufacturing, with a focus on a partnership between subtractive and additive processes. An interesting sidenote was his demonstration of re-enforced concrete machine bases which could be fabricated in relatively short time period to overcome supply chain issues with traditional materials. In many of the stations, ORNL personnel emphasized their attention to understanding the microstructure of the finished workpieces and quality control of porosity. The breadth of the tour stops and numerous technical staff were coordinated by Robert Slattery.
Fourteen technical posters were presented in the UT Conference Center atrium. A fun and well-received session during the first morning was an oral rapid-fire poster introduction. Each poster was introduced in a 3-minute presentation with a strict time-limit. The attendees were able to hear about the subject matter of each poster, learn the principal conclusion, and associate the face of the presenter with the poster for meeting them at the subsequent poster session.
Four Invited Papers highlighted the fourteen technical sessions. Albert To (University of Pittsburgh) led off with a discussion of how new design approaches can address residual strain in an AM workpiece using topology optimization. Machine learning enables the summarization of many simulations that can also be updated using experimental data. There is a tradeoff between the resolution of the simulations incorporated in the design and computation time, which he is addressing using a Modified Inherent Strain (MIS) method. New generations of GPUs offer improved computational abilities. Fred van Keulen (Delft University of Technology) described how the state-of-the-art in topology optimization incorporates AM process physics and could simultaneously optimize the density distribution in a component while also constraining material temperature and thermal gradients. This offers potential for controlling microstructure in addition to weight. Work is still progressing in this area, but computational time and memory requirements are limiting factors.
Afaf Remani (University of Nottingham) presented an invited paper that describes the fusion of multi-sensor data collected from each AM layer combined with post-process volume information. The goal is to address the ‘hard problem’, which she describes as discriminating harmful defects from neutral anomalies in a manufactured part. All parts have numerous features, and fabricating a part with no features is not reasonable. The three layer-by-layer measurement systems include a melt pool monitoring system, fringe projection measurement of the powder bed, and a FLIR measurement of the temperature profile of the broader powder bed. The paper addressed the analysis strategy for combining the various measurements into actionable assessments of defects. Data was presented showing localized cooling rates, melt pool features, and ejected spatter. Layer-by-layer in-process data was correlated with slices of post-process XCT data.
Jason Fox (NIST) presented an invited paper that assesses how segmentation in surface topology characterization can be used for assessing the heat transfer characteristics of an AM-produced surface. Of key interest were methods for assessing the height and areal density of adhered powder particles which offer increased heat transfer efficiency. Amplitude-wavelength analysis and advanced filtering strategies were among the methodologies used for considering how to extract the salient statistics from these highly complex topographies.
The flow of the fourteen technical sessions continued the holistic view of past meetings, beginning with design considerations and ranging to process optimization, metrology, characterization of surface topography, and integration of AM into an integrated manufacturing process. John Taylor invited the speakers to describe how their work enhanced the four pillars of determinism in precision engineering: predictability of error sources, repeatability, quantifiability, and measurability. This led to interesting discussion during networking sessions.
The conference ended with a spirited Closing Session. Each of the technical sessions was considered from “What did we learn?” and “What still needs to be done?” The closing session was appreciated as a means of digesting the firehose of information from the three-day meeting, and offered a means of comparing experiences and observations. Some of the “take-aways” include:
- There is still an enormous challenge in bridging the gap between optimized design and controlling process physics and microstructure, especially with limitations in computational speed and memory
- There is a chronic lack of functional-driven specifications for identifying goals in process design and metrology: How good is good enough?
- Fluid flow and heat transfer provide an excellent means of linking functionality with topography metrics and tolerances
- The past few years have greatly improved the ability to simulate the AM process. This leads to accumulation of simulation data that can be mined for deep learning.
- With AM being a new modality, we need to re-think the problems of assigning tolerances based on “This is the way it has always been done”; there may be new ways to design components that are consistent with as-built AM attributes
- AM is sufficiently mature that we are gathering data and experience
- The ‘hard problem’ discussed by Afaf Remani is important: distinguishing between important critical defects and neutral anomalies
- Storage and processing of the large amount of data from layer-by-layer measurements will be a challenge; will critical components require archival storage of this data?
- Since multiple surface topographies can have the same Ra and demonstrate different functionalities, we need to use better metrics for surface quality
- Future meetings should address powder spreading: E.g., one company was having poor powder spreading, but it was only identified after difficult post-production metrology
- We need to assess the simulation-based training data used in machine learning with respect to realistic fabrication data
- Currently, we do not have an easy approach to propagate uncertainty through a machine learning model
- Future meetings should incorporate a stronger discussion of chemistry, particularly for polymer-based AM
- Since AM creates material, as opposed to only surfaces, it would be better to consider volume integrity
- It is essential to include both polymer-based and metal-based AM in this meeting, because each brings important topics for cross-pollination
- Open architecture machines can lead to a full understanding of the process, even if the approach is not as optimized as a proprietary commercial tool; but there is concern about the acceptance of parts from an open architecture tool by certification committees
- There is a tremendous amount of information from scanning metrology systems, which cannot be ignored even if it is not rigorously traceable; but it may be several years before traceability is demonstrated.
Next year’s meeting will be hosted by euspen and will likely be in the United Kingdom in Fall, 2023. In Summer 2024, the meeting will be hosted by NIST in Gaithersburg, Maryland. Jason Fox (NIST) gave an introduction to NIST and encouraged the attendees to plan to participate.
The proceedings (263 pages) in either digital or printed formats are available from ASPE. The categories of papers are arranged as:
- Design for Manufacturing and Topology Optimization
- Applications of Additive Manufacturing
- Additive Manufacturing Process Physics
- Additive Manufacturing Process Optimization
- Machine Learning & Data Fusion
- Micro-Nano & Lattice Structures
- Characterizing the Performance of AM Machines
- In-Process Metrology
- Topography Characterization & Metrology
- CT to Characterize Inner and Outer Surfaces
- Integration of AM into a Holistic Manufacturing Process