Session I: Industry 4.0 and Learning Control
[divider top=”no” divider_color=”#f10f0f” link_color=”#000000″ size=”7″]Dr. Gijs van der Veen (Equipment & Automation Technologies, Nexperia)
Title: How Learning Control Supports Industry 4.0 in Semiconductor Manufacturing
Description: Industry 4.0 and the ability to schedule production machines flexibly requires that these machines operate with a very similar and consistent performance. Hence, the servo performance of a machine becomes a quality that must be high and consistent within a population of machines. Learning control, with its continuous adaptation to mechanical variations, contributes to this consistency. This talk shows some of the results we have achieved with learning control on Nexperia’s die bonding equipment.
Biography: Dr. Gijs van der Veen joined Nexperia in 2017 as a senior principal dynamics and control developer. He obtained an M.Sc. degree in Aerospace Engineering (2008) and a Ph.D. degree in Systems and Control Engineering (2013), both from Delft University of Technology. As a postdoctoral researcher he was first involved in a mechatronics research project with ASML and subsequently worked as a radiotherapy researcher at the Netherlands Cancer Institute. Currently, he works on potential breakthrough technologies for next generations of Nexperia’s semiconductor assembly equipment.
Chinedum Okwudire (Department of Mechanical Engineering, University of Michigan)
Title: Advanced Feedforward Control as a Service from the Cloud
Description: Control as a Service (CaaS) is an emerging paradigm where low-level control of a device is moved from a local controller to the cloud, and is provided to the device as an on-demand service over the internet. CaaS gives the device access to advanced control algorithms which may not be executable on a local controller due to computational limitations. It also provides other benefits like ease of controller upgrade and machine-to-machine learning, to mention but a few. In this talk, I will summarizes efforts at University of Michigan to develop a CaaS platform for advanced feedforward control of manufacturing machines from the cloud, with initial deployment on desktop 3D printers. I will also present preliminary results on a cloud-controlled desktop 3D printer that demonstrate the potential benefits and challenges of CaaS, along with ongoing and future work.
Biography: Chinedum Okwudire received his Ph.D. degree in Mechanical Engineering from the University of British Columbia in 2009 and joined the Mechanical Engineering faculty at the University of Michigan in 2011. Prior to joining Michigan, he was the mechatronic systems optimization team leader at DMG Mori USA, based in Davis, CA. His research is focused on exploiting knowledge at the intersection of machine design, control and, more-recently, computer science, to boost the performance of manufacturing automation systems at low cost. Chinedum has received a number of awards including the CAREER Award from the National Science Foundation; the Young Investigator Award from the International Symposium on Flexible Automation; the Outstanding Young Manufacturing Engineer Award from the Society of Manufacturing Engineers; the Ralph Teetor Educational Award from SAE International; and the Russell Severance Springer Visiting Professorship from UC Berkeley. He has co-authored a number best paper award winning papers in the areas of control and mechatronics.
Yuyang Wang (Department of Mechanical Engineering, Carnegie Mellon University)
Title: Procedure Control of Nano Materials Design via Reinforcement Learning
Biography: PhD student in Department of Mechanical Engineering, Carnegie Mellon University. Research interests in machine learning in design and optimization.
Description: Fresh and drinkable water supply has been a global challenge nowadays. Precise design of nanoporous materials can create potentials of water desalination in energy-efficient way. In this work, we propose to control the design of nanoporus via reinforcement learning. Namely, at each time step, a RL agent controls the removal of atoms in the nanoporus. Besides, to accelerate the learning process, another machine learning model is built to predict the essential properties of nanoporus: flux and ion rejection rate under certain pressure.
Leontine Aarnoudse (Control Systems Technology, Eindhoven University of Technology)
Title: Long-range piezo-stepper actuators: towards nanoscale accuracy through commutation-angle iterative learning control.
Description: Piezo-stepper actuators are used in many nano-positioning applications due to their high precision and stiffness properties, and the ability to position the mover over an infinite stroke through a walking motion. The walking motion causes disturbances that are repeating in the commutation-angle domain. A new iterative learning control approach is developed that is applicable to long-range piezo-stepper actuators, by exploiting the observation that the disturbance is repeating in the commutation-angle domain. Experimental validation of the framework leads to significant performance improvements.
Biography: Leontine Aarnoudse received the B.Sc degree (2017) and M.Sc degree (cum laude) (2019) in Mechanical Engineering from the Eindhoven University of Technology, Eindhoven, The Netherlands. She is currently pursuing a Ph.D. degree in the Control Systems Technology group within the department of Mechanical Engineering at Eindhoven University of Technology. Her research interests are in the field of control for precision mechatronics, and are mostly centered around the development of learning theory for these systems.
Session II: Advances in Motors
[divider top=”no” divider_color=”#f10f0f” link_color=”#000000″ size=”7″]
Lei Zhou (Mitsubishi Electric Research Laboratories)
Title: Harness the Lag: Precision Positioning with Hysteresis Motors
Description: This paper introduces the research efforts at the Precision Motion Control Lab at MIT on the precision positioning using hysteresis motors. The paper includes two parts. In the first part, we introduce the modeling and field-oriented control (FOC) for hysteresis motors, and presents the experimental tests of the proposed method on three rotary hysteresis motors with different rotor materials. Test results show that all three motors can reach a position control bandwidth of 130 Hz with the proposed methods. The second part briefly introduces the design, building, and testing of a magnetically-levitated linear stage driven by linear hysteresis motors, targeting at the in-vacuum transportation application in semiconductor manufacturing systems. To the best of our knowledge, this work demonstrates the first experimental study on position control for hysteresis motors, and the first linear version of hysteresis motors. It also first demonstrates the use of hysteresis motor in precision motion stages.
Biography: Lei Zhou received the B.E. degree in Control and Instrumentation Engineering from Tsinghua University, Beijing, China in 2012, and the S.M. and Ph.D. degrees in Mechanical Engineering from the Massachusetts Institute of Technology (MIT), Cambridge, MA, USA, in 2014 and 2019, respectively.
Dr. Zhou will be starting as an Assistant Professor in the Department of Mechanical Engineering, The University of Texas at Austin (UT-Austin), Austin, Texas, USA in August, 2020. She is currently a Visiting Research Scientist at the Mitsubishi Electric Research Laboratories. Her research focuses on precision mechatronics, with an emphasis on electromagnetic design, actuators and sensors, precision control, and magnetic suspension.
Wolfgang Gruber (Institute of Electrical Drives and Power Electronics, Johannes Kepler University Linz)
Title: Design and Measurement of a 6-Phase Combined Winding Bearingless Synchronous Reluctance Slice Motor
Description: Bearingless (or self-bearing) motors combine torque and suspension force generation in one common unit. Over the time, nearly all standard drive topologies also got their bearingless counterparts, generating radial suspension forces to stabilize the rotor radially inside the stator and allowing contact-free and, hence, wear-less operation. Using combined winding systems and disk-shaped rotors lead to very compact bearingless motors, stabilizing axial deflections and the tilting passively. However, recently high-temperature surroundings, economic issues and demand for environmental sustainability limit the use of permanent magnets, which are typically implemented in the rotor of such bearingless slice motor systems. Hence, since a few years first concepts without permanent magnets in the rotor have emerged.
We have developed one of the first bearingless synchronous slice motors with combined winding system, featuring only six phases. Only recently it was commissioned and put to full bearingless operation. This session focuses on the design of the prototype, describes the implemented control scheme and presents first static and dynamic measurement results, conducted on a special test rig.
Biography: Wolfgang Gruber received the Dipl.-Ing. (M.Sc.) degree in Mechatronics and Dr. techn. (Ph.D.) degree in Technical Sciences from Johannes Kepler University Linz (JKU), Linz, Austria, in 2004 and 2009, respectively. Since 2012, he has been Assistant Professor and since 2018 Associate Professor of Electric Drive Technology with the Institute of Electrical Drives and Power Electronics, JKU. Since 2004, he has been a Senior Researcher with the R&D company Linz Center of Mechatronics GmbH, Linz, Austria. His research has focused on new topologies for bearingless slice motors, their design, setup, and control. In course of this work, he has developed the following slice motor systems: the bearingless segment motor, the bearingless reluctance motor, the bearingless flux-switching motor, and the bearingless PM Vernier motor. He has authored and co-authored more than 25 journal papers and more than 75 conference papers. Dr. Gruber is the recipient of several international awards, including the Nagamori Award 2015 and the IEEE PEDS Best Paper Award 2015. He is a member of IEEE and VDE.
Tyler Hamer (Department of Mechanical Engineering, Massachusetts Institute of Technology)
Title: Decoupled, Closed-Loop, Multi-DoF Suspension of a Spherical Permanent Magnetic Dipole Actuator
Description: This paper presents decoupled, closed-loop, multi-DoF (degree of freedom) suspension of a spherical, dipole permanent magnet used as the rotor in a reaction sphere bench-level prototype. Specifically, the reaction sphere’s rotor, a 38.1 mm (1.5 in) diameter, spherical NdFeB (Grade 42) permanent magnet (K&J Magnetics SX8), is suspended in all 3 translational DoFs by 12 equidistant cylindrical coils, one centered on each face of the surrounding dodecahedron stator. Due to symmetry of the rotor’s magnetic field and the coils’ layout, applied coil currents are commutated to apply force to the rotor without applying torque, decoupling translation from rotation such that the rotor’s position is controlled with minimal rotation induced. To properly commutate the coils, the rotor’s magnetization axis needs to be known. Twelve equidistant Hall Effect sensors (Allegro A1308KUA-1-T), each placed coaxially within a coil, measure the radial component of the rotor’s external magnetic flux density from which the rotor’s magnetization axis is estimated. The rotor’s angular velocity is also estimated from a backwards difference of the estimated rotor’s magnetization axis. The commutated coil currents are generated by three filtered proportional-integral-derivative (PID) controllers, one for each translation DoF, from an estimate of the rotor’s position, controlling the rotor’s position with a bandwidth of 60 Hz and a phase margin of 30°. Twelve equidistant reflective optical sensors (Fairchild QRE1113GR), each also placed coaxially within a coil, measure their distance from the rotor’s surface from which the rotor’s position is estimated.
Biography: Tyler T. Hamer is a doctoral research assistant in mechanical engineering at the Massachusetts Institute of Technology (MIT) from where he also received his B.S. and M.S. in mechanical engineering. He researches applied mechatronics systems under Prof. David L. Trumper as a member of the MIT Precision Motion Control Lab, deterministically designing actuators, sensors, and entire machines by combining suitable analysis, simulation, and experimentation rooted in 1) cutting-edge and classic control techniques and 2) best practices and fundamental principles of mechanical and electromagnetic engineering. He has applied his research to spacecraft, renewable energy, medical devices, robots, and precision applications such as semiconductor fabrication. Outside of his research, he can be found cooking/bartending, dancing, and playing saxophone or Magic the Gathering.
Benjamin Weinreb (Department of Mechanical Engineering, Massachusetts Institute of Technology)
Title: A Novel Position Sensing System for Bearingless Motors
Description: In this talk, we present a novel sensing system designed to provide position estimates for a bearingless motor system. Bearingless motors combine the function of a magnetic bearing and electric motor to both rotate and levitate a rotor, enabling contact-free operation. The sensing system is required to provide position estimates for commutation and feedback control. We present the design details of the sensing system, characterization of the performance, and preliminary levitation results.
Biography: Benjamin Weinreb is second year Master’s student and Draper Fellow at the Massachusetts Institute of Technology conducting research under the supervision of Professor David Trumper in the Precision Motion Control Lab. His research focuses on the design of a magnetically levitated motor system for pumping applications. Prior to MIT, Benjamin worked as an electromechanical engineer at Draper in Cambridge, MA. He received a B.S.E in Mechanical Engineering from the University of Pennsylvania in 2016.
Session III: Advances in Autotuning and Feedforward Control
[divider top=”no” divider_color=”#f10f0f” link_color=”#000000″ size=”7″]
Alper Dumanli (School of Mechanical, Industrial and Manufacturing Engineering; Oregon State University)
Title: Auto-Tuning of Precision Servo Controllers Suffering from Large Mass Ratio Induced Vibrations
Description: This talk presents an auto-tuning strategy for high precision servo controllers, which suffer from large mass-ratio induced vibrations. The presented auto-tuning strategy is implemented on ultra- precision diamond turning machine, with a spindle/workpiece inertia ratio of 1/80. First, the existing PID controller of the servo system is re-tuned to control low frequency portion of the spindle- workpiece dynamics. This is followed by optimizing a low pass filter within the control loop, which suppresses high frequency dynamics and ensures closed loop stability. Finally, a trajectory pre-filter is optimized with machine-in-the-loop iterations to widen the tracking bandwidth and reduce positioning errors. The proposed strategy is experimentally validated to reduce angular command tracking errors from 4 [mdeg] to 0.225 [mdeg].
Biography: Alper Dumanli received his Ba.Sc. degrees in Mechanical Engineering and Control & Automation Engineering from Istanbul Technical University, Istanbul, Turkey in 2014 and 2015. He received his Ma.Sc. degree in Mechanical Engineering from Oregon State University, Corvallis, USA, in 2018, where he is currently pursuing his PhD degree in Robotics. His research interests include optimal control system design, active and passive vibration mitigation, trajectory optimization and iterative learning control for high precision motion generation mechanisms.
Heejin Kim (Department of Mechanical Engineering; University of Michigan)
Title: Combined Feedforward Tracking Control and Feedrate Optimization – with Application to a Precision XY Stage
Description: Servo error pre-compensation and feedrate optimization are often performed independently to improve the accuracy and speed of manufacturing machines. However, this independent approach leads to unnecessary trade-offs between productivity and quality in manufacturing. In this session, a novel linear programming approach will be proposed for combined servo error pre-compensation and feedrate optimization, subject to contour error (tolerance) and kinematic constraints. The incorporation of servo error pre-compensation into feedrate optimization allows for faster motions without violating tolerance constraints. Experiments carried out on a precision motion stage are used to demonstrate up to 47% reduction in cycle time without compromising part quality using the proposed compared to the independent approach.
Biography: Heejin is a second year Ph.D. student in Mechanical Engineering at the University of Michigan, Ann Arbor. In her research, she focuses on simultaneous optimization of feedrate and servo error in manufacturing machines, ranging from rapid prototyping such as 3D printing to precision positioning. She is also interested in application to large-scale problems with uncertainties in dynamics. Heejin graduated in 2018 with a BS in Mechanical Engineering from Korea University, South Korea, and in 2019 with an MSE in Mechanical Engineering from University of Michigan, Ann Arbor. Prior to joining Michigan, she worked as a research intern in Human Machine Systems Laboratory, Korea University, where her thesis examines development of robot balance feedback system via galvanic vestibular stimulation.
Leon Jabben (MI-Partners)
Title: Feedforward Spectral Tuning and Using Iterative Learning Control For Automated Parameter Fitting
Description: This presentation will analyze the spectral content of acceleration profiles and discusses how the found insights can be used for trajectory generation. The second topic (if time permits) will be how to use ILC with basis functions to minimize the tracking error.
Biography: Leon, born 1974, obtained his PhD 2007. He has been working in the field of mechatronics since 2004. Current fields of interest are: active magnetic bearing technology, dynamic error budgeting and iterative learning control.
Sil Spanjer (Precision engineering, University of Twente)
Title: Adaptive Feedforward Control of a Flexure Based Hexapod
Description: This presentation is treating the design and implementation of an adaptive feedforward controller for a flexible hexapod. This flexible hexapod is designed by the Precision Engineering group at the University of Twente. This hexapod combines a large workspace with high accelerations and the potential for high repeatability. An introduction is given to the working principle and specifications of the flexible hexapod, see figure 1.
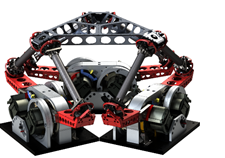
Figure 1: T-Flex – Large range of motion flexure-based hexapod.
Due to the flexible nature of the hexapod, the system has no friction and therefore allows for high repeatability. Proper motion control is required to unleash the full potential of the manipulator. Therefore, a feedback controller is developed aimed to realize this high repeatability. This is appended with a feedforward controller for high tracking performance. To cope with changes in the system, the feedforward controller is made adaptive. An efficient model structure and parameter estimation method allow for real time implementation of the feedforward controller as well as the parameter adaptation.
Biography: Sil Spanjer is a PhD candidate at the University of Twente. His current work focuses on Active Vibration Isolation Control, with an emphasis on robustness. He received his MSc in Mechanical Engineering at the University of Twente. His research interests are adaptive control and mechatronic design.
Session IV: Advances in Mechatronic Design I
[divider top=”no” divider_color=”#f10f0f” link_color=”#000000″ size=”7″]
Rick Baade (Department of Mechanical Engineering, Eindhoven University of Technology)
Title: Vacuum Compatible Contactless Active Magnetic Linear Bearings for High Cleanliness Robotic Applications
Description: A new magnetically suspended linear guide has been designed as part of a high cleanliness, in-vacuum substrate handling robot. The main goals are to minimize contamination generation compared to conventional linear guides and to reduce complexity and cost with respect to typical high performance magnetic levitation systems.
Biography: Rick Baade is a PhD candidate at the Eindhoven University of Technology, Mechanical Engineering department. Previously he worked for two years at VDL Enabling Technologies Group as a mechanical engineer. He graduated from the Eindhoven University of Technology with a masters degree in Mechanical Engineering. Additionally, he is a board member of the Dutch Society of Precision Engineering.
Osama Habbal (Department of Mechanical Engineering, University of Michigan-Dearborn)
Title: Variable Resolution Fused Filament Fabrication (FFF) Printing Using a Variable Orifice Extruder System
Description: This work presents a new method to speed up fused filament fabrication (FFF) additive manufacturing using multiple nozzles with varying orifice diameters and an automatic nozzle switching mechanism.
Biography: Osama Habbal is a graduate student research assistant in Professor Christopher Pannier’s lab at the University of Michigan-Dearborn, working on a master’s thesis in improved extrusion mechanisms for fused filament fabrication. He earned a bachelor’s degree in mechanical engineering from the American University of Sharjah in 2018. He has been working in additive manufacturing since 2015, including working in technical development at the start-up Bright Mind Designs in the United Arab Emirates from 2016 to 2018. The start-up used additive manufacturing for prototyping and product concept validation in artistic, medical, and education applications. Osama has a career interest in academia, focusing on additive manufacturing, machine design, sustainability, and innovation.
Chunjie Fan (Center for Precision Metrology, The University of North Carolina at Charlotte)
Title: Design and Control of a Thermal Actuation System
Description: A thermally actuated single-axis stage is designed and constructed. To increase the temperature of the actuator, induction heating is used, while water-mist cooling is used to decrease the temperature. A combined PID (for heater) and On/Off (for cooler) the control scheme is used. Experimental results are shown to provide precise positioning of the stage under 1 kN pre-load.
Biography: Chunjie(Steve) Fan is currently enrolled as a Ph.D. student, majoring in Mechanical Engineering, at The University of North Carolina at Charlotte under the supervision of Dr. Stuart T. Smith. His research interests include VR/AR, Precision instrumentation design, Precision metrology, and Mechatronics.
Session V: Advances in Sensing and Feedback Control I
[divider top=”no” divider_color=”#f10f0f” link_color=”#000000″ size=”7″]
Brij Bhushan (Department of Mechanical Engineering, Massachusetts Institute of Technology)
Title: Low cost, High dynamic range Position Sensing enabled by oversampling and averaging
Description: Sensors place a fundamental limit on system performance and stability for mechatronic systems with closed loop feedback. This paper describes such an approach to achieving high dynamic range from low-cost sensors using oversampling and averaging. This may be a viable approach to obtain higher performance for low-cost, moderate-performance mechatronic applications.
Biography: Brij M Bhushan is a PhD candidate in mechanical engineering at the Massachusetts Institute of Technology (MIT). His area of research is in applied mechatronics systems under Prof. David L Trumper, as a member of the MIT Precision Motion Control Lab, designing novel mechatronic systems for precision positioning applications. He has applied this research to developing solutions for organs-on-chip devices and semiconductor manufacturing.
Boaz Kramer (ACS Motion Control)
Title: Improved Current Control of Inverter Fed Two-phase Bipolar Stepper Motors Using Repetitive Control
Description: Two‑phase bipolar stepper motors are used extensively in applications that require precise position control at an affordable price. These stepper motors may be driven by three-phase inverters that are commonly used for driving three‑phase brushless motors. The stepper motors are known to be plagued with resonances, oscillatory behavior, and acoustic noise problems. Their performance is strongly influenced by the motor’s current waveforms.
Typically driving the motors with sine‑wave currents (aka micro‑stepping) will lead to smoother motion and better performance. However, the motor currents are usually far from ideal and suffer from various harmonic distortions caused by drive and motor imperfections. The Proportional‑Integral (PI) Controllers typically used in the Field‑Oriented Current Control scheme are inadequate to cope with these distortions due to their limited control bandwidth and the relatively high frequencies of the harmonics.
The session recommends a Repetitive Control approach to solve these issues and significantly improve the motor current waveforms and overall performance. A standard time‑indexed Repetitive Control will be explored first. Following the realization that the disturbances are reproducible and have fixed periods in the angle domain, an Angle‑Domain Repetitive Controller will be proposed.
Actual experimental data of the prescribed control scheme will be presented.
Biography: Boaz Kramer received his B.Sc. degree (cum laude) in 1995 and M.Sc. degree in 2001, both from the Department of Electrical Engineering of the Technion, Israel Institute of Technology.
Since 2001 he has been working at ACS Motion Control, a global company providing high performance motion control solutions to OEM machine builders serving semiconductor, FPD, Medical, Digital Printing, Laser Processing and Electronic Assembly industries. He is responsible for the development of new advanced control algorithms and presently serves as Vice President of Control, Support and Applications.
Paul Köchert (Physikalisch-Technische Bundesanstalt (PTB))
Title: Dynamics and Control of the PTB Nanometer Comparator
Description: The presentation gives insights into a length measuring machine at the national metrology institute of Germany.
The so-called Nanometer Comparator has been upgraded to provide a highly linear behavior of its subsystems (measurement, drive & control system) over the entire measurement range of 600 mm. We show that the position of test specimens can now be controlled on the sub-nanometer level without compensation methods (Heydemann correction) and disturbance observers (Kalman filtering).
Biography: Paul Köchert was born in Ilmenau, Germany, in 1982. He received the Dipl.-Ing. and Dr.-Ing. degrees in electrical engineering from the Ilmenau Univ. of Technology, Germany, in 2008 and 2018, respectively. He is currently a research fellow at the Department of Multiwavelength Interferometry for Geodetic Lengths at the PTB. His current research interests focus on FPGA-based signal processing methods for interferometric systems, laser stabilization and motion control applications.
Liam G. Connolly (Walker Department of Mechanical Engineering)
Title: Heuristically Optimized H-Infinity Synthesis for the Real-time Positioning of a Tip-based Measurement Device
Description: This presentation demonstrates the use of a heuristic, multi-objective optimization process to procedurally generate a control system for the real-time positioning of an atomic force microscope (AFM) probe for process measurement in roll-to-roll nanomanufacturing. To achieve this, the system must regulate probe trajectory to match web velocity as sensed by the angular rotation of an unwind roller. Optimizing controller performance for a similar system would typically mandate the use of a more traditional optimal control technique, such as iterative learning control (ILC) or finite-horizon linear quadratic programming, but as a-priori knowledge of the precise trajectory required is not available and computational effort limited by a low-cost FPGA, H-infinity control is chosen. The various parameters used to define the high- and low-pass filters used as the weights which drive mixed sensitivity H-infinity control synthesis are chosen by the optimization algorithm to minimize both maximum controller effort and a normalized controller error metric generated with a simulated typical measurement cycle trajectory. As a result of the robust nature of H-infinity synthesis, the generated stabilizing controller should also be resistant to variations in system parameters such as moving mass, flexure stiffness and actuator sensitivity which are not accurately captured in the experimentally identified 4th order model. A set of pareto-optimal controller candidates is thereby generated, and the advantageous performance of this method compared to traditional, loop-shaped, H-infinity design is shown, all without need for the typically experience driven trial-and-error process of choosing H-infinity weighting functions.
Biography: Liam G. Connolly received his B.S. in Mechanical Engineering from Tufts University in 2016 and his M.S. in Mechanical Engineering from The University of Texas at Austin in 2019 with a focus on precision machine design. Liam is currently an NSF Graduate Research Fellow pursuing his Ph.D. in Mechanical Engineering at UT Austin’s Nanoscale Design and Manufacturing Lab and the NASCENT NSF Nanosystems Engineering Research Center. His research focuses on machine & mechatronic design and data analysis for tip-based nanometrology in high-throughput R2R fabrication and very large area measurements. Outside of research, Liam is an avid sailor, shade-tree-mechanic, and unsuccessful amateur racer in both disciplines.
Session VI: Advances in Sensing and Feedback Control II
[divider top=”no” divider_color=”#f10f0f” link_color=”#000000″ size=”7″]
Fangzhou Xia (Mechatronics Research Lab in Department of Mechanical Engineering, Massachusetts Institute of Technology)
Title: Model and Controller Design for High-speed Atomic Force Microscope Imaging and Autotuning
Description: Atomic Force Microscope (AFM) is a powerful nano-scale surface measurement instrument. However, significant operator experience is needed for successful imaging. Parameters of the PID controller for probe deflection or oscillation regulation are tuned by the operator based on visual inspection of the trace and retrace tracking performance. With the development of high-speed AFM and for the purpose of operation overhead reduction, automated parameter tuning of the controller is needed. In this work, we propose a unified framework with various control and image generation improvement methods for contact mode AFM, starting first with an automated PID controller tuning and scan speed adjustment method. Second, we discuss three methods to improve imaging performance including location-based sampling, line-based feedforward and error-corrected image generation. Third, in cases where topography variation and material properties are non-uniform across the sample surface, a single neuron PID is designed for model-free adaptive tracking. With a lumped parameter AFM model created in Matlab Simulink, the proposed algorithms are evaluated in simulation to demonstrate their effectiveness. The methods are summarized into a unified framework where methods can be automatically selected after initialization to improve AFM imaging performance.
Biography: Fangzhou Xia (SM’17) is a Ph.D. candidate in the mechanical engineering department of Massachusetts Institute of Technology (MIT) specialized in the field of control, robotics and instrumentation. He obtained his Master’s degree in the mechanical engineering department of MIT in 2017. He obtained his dual bachelor degree in mechanical engineering from University of Michigan, Ann Arbor and in electrical and computer engineering from Shanghai Jiao Tong University in 2015. Fangzhou is currently a research assistant in the Mechatronics Research Lab and a teaching assistant for the introduction to robotics class at MIT. Fangzhou is interested in precision mechatronic system with physical intelligence, advanced motion control and nanorobotic device design.
Álvaro Fernández-Galiana (Department of Mechanical Engineering, Massachusetts Institute of Technology)
Title: Implementation of Length Control of an Optical Cavity using Second-Order Transverse Modes
Description: Optical cavities are used in a variety of applications due to their ability to enhance the optical field. However, this enhancement is only present when the optical length of the cavity is stabilized (locked). We present the development and testing of a method to generate the cavity length error signal using transverse Laguerre-Gaussian (LG) modes of order two. The primary advantage of this locking scheme lies in its simplicity combined with the capability of locking at the peak of the resonance. The presented technique is of special interest to compact applications, since it requires a minimal number of components.
Biography: Álvaro Fernández-Galiana is a PhD candidate in Mechanical Engineering at the Massachusetts Institute of Technology. He works as a research assistant at the Laser Interferometer Gravitational-Wave Observaroty (LIGO) with Prof. Matthew Evans and Prof. Nergis Mavalvala. Alvaro’s research focuses on the design of precision instruments, including vibration isolation stages and compact optical devices. Before joining MIT, he received a M.Sc in Mechanical Engineering from the Polytecnic University of Catalonia-UPC (Barcelona, Spain) and a M.Sc in Aerospace Engineering from ISAE-Supaero (Toulouse, France).
Fabrice Matichard (LIGO Laboratory, MIT, Caltech)
Title: Active Optical Mode Matching for the Quantum Squeezing Cavaties and Upcoming LIGO Upgrades
Biography: I joined the LIGO group at MIT as a Postdoc fellow in 2006. I have been a Senior Research Engineer with the California Institute of Technology since 2011, leading engineering projects in the field of active vibration isolation, quantum optics and adaptive optics.
Description: As the laser beam travels through the LIGO detector, it must be mode matched to the various cavities. This talk will present the adaptive optic that has been developed to control the de-focus mode. It uses a flexure mechanism that converts PZT transnational force into mirror curvature with minimum generation of higher order aberrations. The talk will cover the concept of mode matching, the mechanism design and test results.
Daegweon Koh (School of Mechanical Engineering, Gwangju Institute of Science and Technology (GIST))
Title: Dynamic Characterization of Lapping Manipulator
Session VII: Modeling and Control of Precision Machines
[divider top=”no” divider_color=”#f10f0f” link_color=”#000000″ size=”7″]
Pablo Hernández-Becerro (Inspire AG Technoparkstrasse 1)
Title: Reduced thermo-mechanical model of a rotary table of a 5-axis precision machine tool
Description: Among the different error sources, thermally induced deviations are the major contributor to geometrical errors in manufactured parts. Thermo-mechanical models, based on the Finite Element discretization of the heat transfer and elasticity equations, describe the temperature distribution and the associated structural deformation. However, evaluating thermo-mechanical models is computationally expensive, limiting applications that require a large amount of model evaluations, as well as the possibility of real time predictions. Therefore, we present a reduced-order thermo-mechanical model of a precision a 5-axis machine tool. We investigate the thermal errors associated to the rotary table, the C-axis. We develop a reduced-order thermo-mechanical model in a dedicated software environment, MORe, developed in our group at ETH Zurich. We compare the simulated and measured thermo-mechanical response during the rotation of the C-axis. Once the thermo-mechanical model is validated, we use the information of the physical model to improve the thermal error compensation strategies.
Biography: I studied Mechanical Engineering at the University of the Basque Country (Spain), where I received my MSc degree in 2014 specializing in machine tools and manufacturing. In 2014, I moved to Zürich to start a graduate program with a focus on precision engineering. In 2016, I started my doctoral studies at ETH because of the exciting opportunity to join a project supervised by Prof. Konrad Wegener on thermo- mechanical behavior of mechatronic systems. During my PhD, I had the opportunity to do research on the measurement of thermal errors, compensation, and simulation of the thermo-mechanical behavior of machine tools. Just a month ago, in April 2020, I defended my PhD thesis. I am currently looking for a new research position where I can apply the skills that I developed in my previous research projects. During my free time, I love hiking in the Swiss Alps and playing piano.
Renan Geraldes (Brazilian Synchrotron Light Laboratory (LNLS),Brazilian Center for Research in Energy and Materials (CNPEM))
Title: Dynamic Error Budgeting in the Development of the High-Dynamic Double-Crystal Monochromator for Sirius Light Source
Description: This work presents the Dynamic Error Budgeting (DEB) workflow applied to the High-Dynamic Double-Crystal Monochromator (HD-DCM), which is an energy-selecting X-rays optical instrument that has been developed by the Brazilian Synchrotron Light Laboratory for Sirius Light Source. Being the first DCM to be implemented with a low-stiffness mechanical design concept in a high closed-loop control bandwidth, nanometer-level positioning performance, with improvements by factors of 4 and 100 with respect to state-of-the-art monochromators, in fixed and scanning modes, respectively, could be achieved. The DEB methodology is demonstrated via a 6-degree-of-freedom (DoF) mechatronic model with special attention to the disturbance models and the predicted performance, which can finally be compared with experimental results.
Biography: Renan Geraldes joined the Mechanical Design Group of the Brazilian Synchrotron Light Laboratory (LNLS) in 2011. Since 2013, he is a member of the Beamline Engineering Group, designing advanced beamline instruments for the 4th-generation-light-souce Sirius. He received his Master’s degree in Physics with emphasis in Scientific Instrumentation from the Brazilian Center for Research in Physics (CBPF) in 2015. He is currently a PhD candidate in Control Systems Technology at the Eindhoven University of Technology (TU/e).
Ricardo Caliari (Brazilian Synchrotron Light Laboratory (LNLS), Brazilian Center for Research in Energy and Materials (CNPEM))
Title: Loop-shaping Controller Design in the Development of the High-Dynamic Double-Crystal Monochromator at Sirius Light Source
Description: Present the application of loop-shaping controller design technique in the development of the High-Dynamic Double Chrystal Monochromator for the Sirius light source in Brazil, the new fourth-generation synchrotron.
Biography: Head of the Mechatronics Instrumentation and Assembly Group, Control Engineer by the University of Campinas. With the previous 5 years of experience in the industry environment in Brazil and Europe, since 2015 working in the development of the cut-edge technology of the new Brazilian Synchrotron Light Source, applying high precision engineering concepts to develop the new generation beamline instruments.
Marcelo Moraes (Brazilian Synchrotron Light Laboratory (LNLS), Brazilian Center for Research in Energy and Materials (CNPEM))
Title: The FPGA Control Implementation of the High-Dynamic Double-Crystal Monochromator at Sirius Light Source
Description: The 4th generation synchrotron light sources increased significantly the demand of precision between multiple coordinated optical devices. Beyond the in-position control, it is common to perform scans by varying the position of the sample or the optical elements. The HD-DCM was developed to improve both the positioning performance in fixed and scanning modes, and could reach factors of 4 and 100, respectively, with respect to the state-of-the-art monochromators.
After the concepts validation in a rapid control prototyping platform, the controller was migrated to a rugged platform, more adequate to the beamline environment and long-term execution. The migration process involved a full review of software architecture, quantization error analysis and tools for integration between Matlab and LabVIEW. After platform migration, the FPGA implementation was guided by resources optimization and critical path timing concerns.
Biography: Marcelo Moraes is a mechatronics engineer who worked for eight years as industrial automation integrator for beverage, health care, chemistry, oil and gas industries, mainly. In 2016 he started working for the Brazilian Synchrotron Light Laboratory and is the head of the Control and Integration Group, with focus on motion control. In the last years, he have been working with software and firmware development for high precision applications.
Session VIII: Advances in Mechatronic Design II
[divider top=”no” divider_color=”#f10f0f” link_color=”#000000″ size=”7″]
Jon Kelly (The Diamond Light Source, Harwell Science Campus)
Title: Delta Robot Combining Millimetre Travel With Nanometre Performance
Description: My talk is about the design, build and test of a sample stage for a Synchrotron X-ray microscope.
Biography: I am a Senior Mechanical Project Engineer. I have been working at the Diamond Light Source Synchrotron for almost 10 years. I only moved into the world of Mechatronics Last year.
Heebum Chun (J. Mike Walker 66’ Department of Mechanical Engineering, Texas A&M University)
Title: Thermally Stable Precision Motion and Positioning Mechanism
Description: While, in precision engineering, thermal stability has always been important for achieving high precision in the mechanical, electrical, or chemical systems. The performance of systems highly depends on thermal stability. Achieving high precision in the mechanical system is hampered by the generated heat because the components in the machine system such as frames, guides, sensors, and motors are susceptible to thermally deform. Therefore, novel methods are required for the precision machine systems to sustain the environment to be most thermally stable. This research investigated a novel mechanism to manage control motion and thermal issues of nanopositioning systems that use additively manufactured flexure-based mechanism by flowing fluid into the internal fluidic channels of the flexure-based compliant structure. As a result, the media flowing through fluidic channels lower the increased temperature and reduce the error in thermal displacement caused by heat generation. The developed technology is expected to meet the growing need for accuracy and precision in nanometer motion control and achieve the environments that are thermally stable in an effective, low-cost, and convenient way.
Biography: Heebum Chun is currently enrolled as a graduate student at Texas A&M University under Dr. ChaBum Lee’s supervision and majoring in Mechanical Engineering. Before he joined Texas A&M University, he earned a bachelor’s degree at the University of Alabama. His research interests are precision mechatronics, controls, manufacturing, and metrology. He is trying to seek any possible approaches to solve the current manufacturing problems and to create new manufacturing methods and processes to push limits.